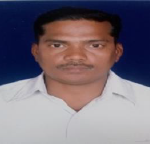
PRASHANT GOVEKAR
About Candidate
I having more than of 3 years’ Experience in QA/QC Inspector Welding, Piping, Mechanical, NDT, Inspection Engineer for Pipe mill inspection, Pipeline, Fabrication, Construction, Materiel Testing, Coordination, Painting/Coating, TPI, Vendor Inspection, Surveyor, Lead Auditor for the Upstream, Downstream and Midstream Such as Manufacturing Industries, EPC Projects, TA etc.Good knowledge in conventional NDT & Automatic NDT method
Education
Experiences
• Inspection of Tank plumpness, roundness, misalignment, joint ID marking, peaking, and banding. Visual inspection for defects in the weld. • Inspection of the bottom weld by using Vacuum Box test to ensure the soundness of bottom weld. • Review ITP, WPS, Weld map and tank drawings compliance to project specification and API TANKS. • Review Hydro test procedure and ensure for mechanical clearance and test is conducting as per approved procedure. • Review of documents like QAP,ITP and QA/QC Procedures. • Material Inspection (i.e. Pipes, Plates, Fasteners, Fittings Forgings etc.) as per applicable code. • Stage inspection as per approved drawing, QAP,ITP and QA/QC procedures and applicable codes. • Issue of Inspection Release note after successful completion of final inspection. • Witness of Hydro tests and Pneumatic tests of Piping’s & Equipment’s. • To check of orifice flange inspection and pipe flange alignment report. • To study the P&ID and other circuit diagrams in the test pack. • Monitoring the calibration of test instruments and equipment’s. • Review and Interpretation of RT films as per ASME B 31.3,SEC V,SEC VIII,API 1104 & AWS D1.1. • Inspection and testing activities as per the inspection procedures. • To check the fit up stage prior and confirm that root gap, off set, bevel angle are with in acceptable limit. • To witness preheating process and verify the chart. • Witnessing of activities like PQR, Welder’s qualification Tests, Mechanical testing and preparation of PQR records and WQT certificates. • Review and Witness that the welding parameters are confirmed to WPS in during welding. • Review and Check the temperature of electrode as per the WPS. • To do the visual inspection after completion of the welding. • Witness and review the post weld heat treatment process and verify the chart. • To witness MPT, LPT of fillet weld joints, butt weld joints and check the surface & sub surface defect.
• Review/Approval of Inspection & Test Plans, Quality Control procedures, Method statement/s, Welding Procedures etc. • Monitoring / Witnessing all the Welding, Fabrication & Erection related activities as per client approved Inspection & Test Plans/Quality Control procedures. • Inspection of incoming materials and reviewing test certificate as per code • Inspection of piping materials identification as per isometric drawings. • Witnessing of activities like PQR, Welder’s qualification Tests, Mechanical testing and preparation of PQR records and WQT certificates. • Stage wise inspection before, during and after fabrication. • Prepare and maintain all the quality documents in accordance with client requirements. • Liable for surveillance, monitoring, and review of all day to day documentation during piping Fabrication and Erection phase. • Preparation and Review of Welding Procedure Qualification and welder qualifications. • Looked after selection of electrodes for welding various types of steels, welding procedure and welder’s performance qualification test as per ASME SEC IX. • Monitoring of welder performance and controlling weld repair by analyzing the root cause and implementing corrective action to prevent recurrence. • Ensure safe and proper welding practices are employed at all times; confirmed material identity according to approved drawings, reviewed Manufacturing Test certificates of consumables, etc. • Taken care of verification of the calibration certification of welding machines / Inspection equipment’s as per requirements. • Looked after consumable used in welding to ensure compliance with specification and monitored welder’s performance to ensure that they are performing within the limits of their qualifications. • Monitoring the log for project Observation and NCR’s and ensuring that all observations and NCR’s are closed properly. • Witnessing of fit –up. Check the correct pre-welding and In-process distortion control. • Monitoring of welding activities of sub-contractors piping and welding work. • Carry out visual inspection of the weld joint. • Co-ordination, Request for Client Inspection at stages. • Preparation of punch-list after line walkthrough with client and verification of punch-list completion. • Material list prior to Receiving Piping Isometrics and verification of Revisions, Preparing Fabrication. • Responsible for the fabrication and construction of pipes to its exact location / area as per drawing. • Stage-wise inspections and fabrication of piping, structures and installation of equipment. • Check, verify/review fabricated/erected or installed lines as per latest isometric drawing for construction. • Quality check on the piping material/ accessories and installation as per the Quality Specifications/ Manual.
• Involved in Inspection as well as NDT Jobs like UT, MT, PT on Behalf of INTERX at KNPC KUWAIT SHUTDOWN JOB. • Performed NDT and visual testing for various clients in shut down. Involved in UT, MT, PT and visual Inspection of • Performing VT, PT, and MT in Boiler, Tank, and Vessels and on Weld joints. • Scanning of pipelines, bottom floor plates of tanks, vessels, heat exchangers, Butt weld joint. • Inspection of Fit up, DP test of root welds and weld visual • Calibration and interpretation during Ultrasonic Testing.
Carried out Ultrasonic Thickness measurement of pipelines, Corrosion check on pressure vessels, tanks, exchangers, column etc., • Radiography testing for small bore piping & butt weld piping during execution • UT lamination check on raw materials • Carried out thickness survey on Piping and Equipment in Refinery • Carried out Profile Radiographic Test on Small Bore Fitting in Refinery in service Piping • Familiar in API, ASME B31.3, AWS D1.1 and ASME Sec VIII Standards • UT Lamination and thickness survey of ages both erosion and corrosion components, vessels, piping and tubing of petroleum, refinery, Power and Chemical Industries • Preparation and submission of reports & Co-ordination with clients • Coordination the field inspection activities of Piping as per approved welding procedure specification. • Witnessing Procedure Qualification records (PQR) and Welder Qualification. • Witnessing and reviewing of NDT Report’s such as RT, UT, MT and PT. • Preparation of punch list and witnessing the pressure tests. • Submitting test packs for final certification • Ensuring that welding meet with Client Specification, Project scope and Drawings. • Preparing Inspection Documents for finished jobs and maintains test records. • Visual Inspection of fit-ups, Root and final welding of Groove welds and fillet welds. • Interpretation of Radiographic Film as per ASME/ANSI B 31.3.
• Review Project Documents Such as PO, ITP, PIM etc. • Witness of Transverse Tensile Test, Impact Test, Chemical Analysis. • Witness of UT of Edges 50mm and 60% of Plate Surface. • Witness of Edge Milling and Pipe Forming Process. • Witness of WPS, WPQ, PQR as per ASME SEC XI/ API 5L Annex C & D • Witness of Continuous Tack Weld and Automatic Submerged ARC Welding. • Witness of Cold sizing & Cold Expansion. • Witness of end Preparation like Bevel angle and Root face. • Visual Inspection for Defects, Misalignment and Height of Weld Beads. • Inspection for Dimensions, Length, Weight, Straightness etc.