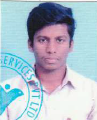
NIRMAL KUMAR.C
About Candidate
Dynamic Engineer and Motivated Professional with More than 6 Years of experience as Inspection Engineer in Oil & Gas Industry. Seeking Assignments in Onshore / Offshore – Welding / NDE / Pressure Vessel / Piping Projects / Storage Tank’s – for Quality Control and Quality Assura
Education
Experiences
Determination of Minimum required thickness/MAWP/Remaining life/Corrosion rate for piping, pressure vessel and AST as per API code. Establish next scheduled Inspection interval for plant equipment as per API code. Prepare/Review the calculation of Re-rating/Alteration/Repair which meets the In-service code. Perform Internal/External/On-Stream Inspection for Static Equipment’s as per API Codes. Perform the Internal Inspection of all kind of Static Equipment Such as Reactors, Heat Exchangers, Pressure Vessel, Columns and Tanks during the shutdown and Assessment of Present Condition. Perform Internal inspection of Distillation column and asses the condition of Distributor piping, Tray deck, Tray valve, Nozzle bore, Random & structured packing, Feed inlet line, Liquid collector chimney tray, Demister pad, Tray support ring etc. Perform the External Inspection of Static Equipment and assess the condition of concrete support Anchor Bolts, Grounding Connection, Nozzles, Skirt Supports, Structural and Protective Coating/Insulation. Inspection of Tube Bundles Components such as Tube sheet, Tubes, Tie rods, Spacers and Tube Baffle Plates, Support Plates and Impingement Plates. In-depth knowledge in the selection of Repair technique and its engineering evaluation/Limitation related to damage mechanism as outlined in ASME PCC-2. Carry out Internal/External inspection of vessels/drums, column, reactor, heat exchanger, fin fan cooler and AST during Turn Around maintenance. Knowledge and Remedies of Damage mechanism in equipment such as Chloride SCC/Amine cracking/Hydrogen Blistering/HIC/SOHIC/Caustic SCC/CUI/Sulfidation/Carburization/Temper embrittlement as per API 571. Witnessing Hydro/Pneumatic test of Heat exchanger/Piping and Witnessing vacuum box test/Diesel test/Air test on repaired weld joints. Knowledge of both core and Advanced NDT techniques (IRIS/ECT/MFL) and their application and limitation in conducting fixed equipment/Fitness for service damage assessment Inspection of valves (Globe/Plug/Gate/Check/Ball) and witness valve pressure test such as Shell test, Back seat test, & Closure test as per API 598. Support turn-around through engineering package review, Drawing review, ITP & Scope development during discovery. Through knowledge in preparing WPS/PQR with respect to essential/non-essential variables as outlined in various codes such as ASME SEC IX, AWS D1.1and API 1104. Conduct WQT for various WPS and establish welder qualification range as per ASME SEC IX, AWS D1.1and API 1104. Conversant with welding inspection, PWHT, Hardness measurement and PMI. Extensive knowledge in selection of welding consumables with respect to base materials and welding process. Conversant with Blasting and coating Inspection such as surface cleanliness/Profile check/WFT&DFT check/Adhesion test/Holiday test etc. Perform External/On stream/Internal Inspection on AST and evaluate the suitability of an existing tank for continued service based on inspection findings. Establish NDT requirement on welded joints in various situation such as major repair/ alteration, minor repair/ alteration and reconstructed tank. Determination of minimum required shell thickness, maximum fill height, corrosion rate, remaining life, calculation and establish the next inspection interval. Establish the minimum required thickness of bottom plate at next inspection interval based on MFL and Ultrasonic scanning report. Inspection and Installation of Pressure Regulating Devices as per API and ASME Code.